Mangueras hidráulicas de media y alta presión: clasificación y usos
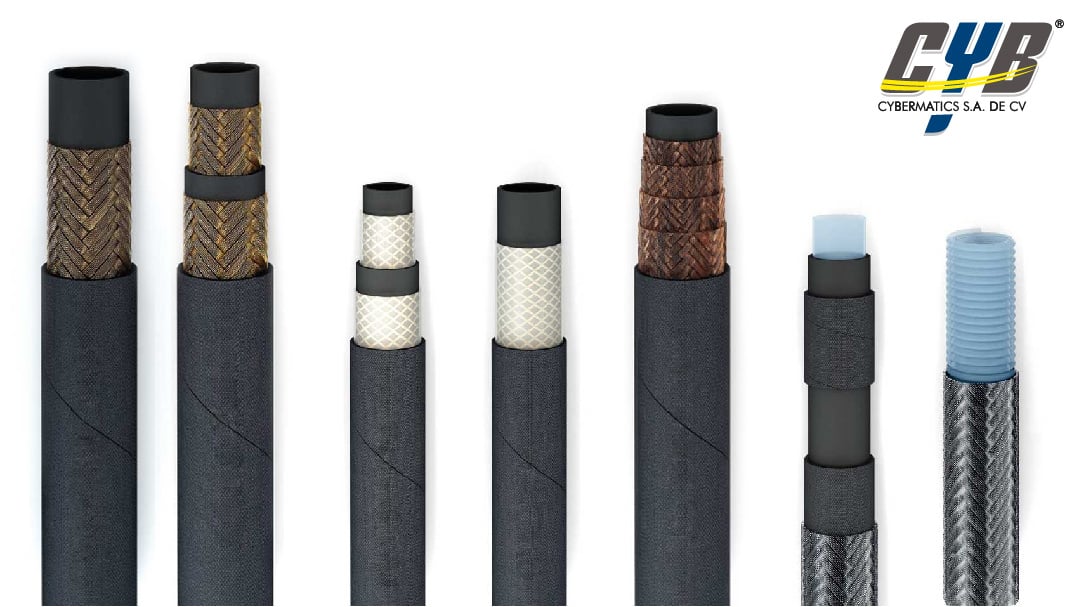
Sistemas hidráulicos y su clasificación
Los sistemas hidráulicos convierten la energía de un líquido en energía mecánica o movimiento. Gracias a la incompresibilidad de los líquidos, estos sistemas manejan presiones considerablemente superiores a los sistemas neumáticos. Esta característica también es aprovechada para realizar acciones con gran precisión, en contraste con la velocidad que ofrecen los sistemas neumáticos.
Debido a estas características, los sistemas hidráulicos son diseñados en una vasta diversidad de configuraciones en aras de satisfacer las complejas necesidades industriales. Una de las principales características que clasifican a los sistemas hidráulicos es la presión de trabajo que estas pueden manejar.
- Baja presión: Se considera baja presión a los sistemas que operan hasta 1,60 [MPa] (230 [psi]). Estas presiones son típicas en aplicaciones domésticas, y de irrigación de cultivos. También es una presión manejada en circuitos neumáticos de gran envergadura como los sistemas de transporte de materiales a granel.
- Media presión: Los sistemas que trabajan entre 1,60 y 10 [MPa] (230 – 1.450 [psi]) son considerados mediana presión. Este rango de presiones es común en sistemas de frenado automovilístico o sistemas de transporte; también es usado en maquinaria industrial de uso general.
- Alta presión: El rango de presiones que va desde los 10 hasta los 100 [MPa] (1,45 – 14,50 [ksi]) se considera alta presión. A partir de este punto, el riesgo aumenta considerablemente, por lo que el factor de seguridad es un elemento clave en el diseño de los sistemas que usan alta presión. Algunas aplicaciones que se encuentran en este rango son las prensas hidráulicas, equipos de fracking, y chorros de agua a alta presión para corte de materiales.
- Extrema presión: Finalmente, los sistemas que exceden los 100 [MPa] (> 14,50 [ksi]) son considerados de extrema presión. Este rango de presión está reservado para maquinaria especializada, como los equipos de corte a chorro de alta potencia, decapado de piezas metálicas, y pruebas de ingeniería a presión.
Por lo tanto, concluimos que la selección de los componentes que formarán parte de nuestro sistema hidráulico es un factor vital. Estos deberán ser capaces de soportar la presión que maneja nuestro sistema, además de ofrecer una buena respuesta a demás factores adversos. Uno de los componentes más comunes en cualquier sistema hidráulico son las mangueras, las cuales se fabrican bajo diferentes estándares para cumplir con los requisitos hidráulicos más desafiantes. Entre estos estándares de fabricación, destacan 3 modelos.
SAE 100R1 – EN 853 1SN
La manguera SAE 100R1 está compuesta por un núcleo se goma sintética resistente al agua, aceites y derivados de petróleo. Adicionalmente, esta reforzado con una malla de acero trenzado, que incrementa su resistencia a la presión. Finalmente, esta manguera es protegida por una cubierta de goma sintética resistente a la abrasión, aceite, y a la intemperie. Esta manguera no requiere que se retire parte de su cubierta protectora para ser sometida al proceso de crimpado. Debido a sus características, esta manguera cumple con las exigencias de las aplicaciones de media presión. Algunas de estas aplicaciones son el transporte de fluidos en maquinaria industrial, y elevación de cargas en la industria agrícola.
SAE 100R2 – EN 853 2SN
Similarmente a la SAE 100R1, esta manguera cuenta con un núcleo y revestimiento de goma sintética resistente a la abrasión y derivados del petróleo, tampoco requiere remover el revestimiento para crimpar. Sin embargo, en este caso, esta manguera cuenta con dos refuerzos de malla de acero trenzado, lo que incrementa significativamente su resistencia a la presión respecto a la manguera SAE 100R1. Esta manguera puede ser usada en aplicaciones de mediana presión que requieran un elevado factor de seguridad, y de igual manera tiene cabida dentro de las aplicaciones de alta presión. Gracias a sus componentes, este producto puede ser usado en el transporte de productos a base de petróleo como aceites, combustibles y lubricantes, lo que lo hace un elemento clave en la industria minera, metalúrgica y petrolera.
SAE 100R12 – EN 856 R12
Finalmente, hablaremos sobre la manguera más robusta de las tres. Con un refuerzo compuesto de cuatro espirales de acero de alta resistencia, esta manguera ofrece la mayor resistencia a la presión de todas, por lo que se reserva para aplicaciones de alta presión. Debido a las capas de refuerzo, este producto se emplea primordialmente en procesos sometidos a picos de presión frecuente, como es el caso de los taladros hidráulicos usados en la industria minera. Adicionalmente, esta manguera también cuenta con un núcleo y revestimiento de goma sintética, similar al de las mangueras SAE 100R1 y SAE 100R2.
Comparativa entre mangueras
Ya cubierto los estándares de fabricación de estas mangueras, procederemos a analizar el comportamiento de estas mangueras frente a la presión, y como esta es afectada a medida que variamos la sección transversal de cada una.
Presión de trabajo
La presión de trabajo se refiere a la presión máxima a la cual puede trabajar una manguera hidráulica para maximizar su desempeño y vida útil. Lo que quiere decir que, al exceder este nivel de presión, las mangueras empiezan a experimentar una reducción significativa de su vida útil, más no quiere decir que esta vaya a fallar. A continuación, se muestra una tabla con las presiones de trabajo típicas.
Como podrá apreciar, a medida que reducimos la sección transversal de las mangueras, es decir, reducimos el diámetro de estas, la resistencia a la presión se reduce. Típicamente, cuando se habla de la presión máxima de trabajo de las mangueras hidráulicas se hacer referencia directa al diámetro más pequeño disponible.
Adicionalmente, se observa como la resistencia a la presión varia considerablemente entre cada modelo de manguera. La única excepción se encuentra en las mangueras de 3/8" respecto a los modelos SAE 100R2 Y SAE 100R12. No obstante, la diferencia principal en este diámetro radica en la resistencia a los impulsos de presión.
En este gráfico, podemos entender el comportamiento de la vida útil de las mangueras hidráulicas y como se ve afectada con los cambios de presión. Se observa que, si a esta se le aplica un aumento de 1,25 veces la presión de trabajo recomendada, la vida útil se desploma hasta una 50%.
Impulsos de presión
Similar a las fallas por fatiga que pueden experimentan los materiales sólidos, las mangueras hidráulicas pueden ser sometidas a impulsos o picos de presión que acorten considerablemente la vida útil de estas. Para asegurar la máxima vida útil, estas mangueras son sometidas a una prueba de pulsos de presión en la cual no deben presentar síntomas de agrietamiento, o ruptura. En este procedimiento, la manguera es sometida a una frecuencia de impulsos de presión del 133% la presión de trabajo y a una temperatura de 100 [°C] (212 [°F]). Tanto las mangueras SAE 100R1 y SAE 100R2 deben ser capaces de soportar 200.000 impulsos durante la prueba, mientras que la manguera SAE 100R12 deberá soportar 400.000 impulsos. Lo que hace a la manguera SAE 100R12 un producto de extrema robustes y calidad.
Presión de prueba
Similar a la prueba de impulsos, las mangueras hidráulicas son sometidas a un ensayo no destructivo llamado prueba de presión. En esta prueba, las mangueras son sometidas a una presión entre 1,75 y 2 veces la presión de prueba durante un tiempo de entre 30 y 60 segundos. Durante este ensayo, la manguera no deberá agrietarse, ni presentar síntomas de fuga de fluido.
Presión de ruptura
Finalmente, las mangueras hidráulicas son sometidas a una prueba destructiva para determinar la presión de ruptura del producto. En este ensayo, la manguera es sometida a una presión que aumenta con el tiempo hasta que la manguera estalle o presente síntomas de ruptura. El valor obtenido de esta prueba es típicamente 4 veces la presión de trabajo de la manguera. Es decir, que la relación entre la presión de ruptura y la presión de trabajo, mejor conocido como factor de seguridad, es de 4.
Conclusión
Como podrá observar, las mangueras hidráulicas destinadas a las aplicaciones de mediana y alta presión son fabricadas bajo los más estrictos estándares y sometidas a rigurosas pruebas con tal de satisfacer las diversas y complejas necesidades industriales. A la vez que salvaguardan no solo la integridad de los sistemas de los cuales forman parte, sino también la de los operadores que laboran en las inmediaciones del sistema.